Calcium Carbonate Dry Grinding Production Line
The processing of ground calcium carbonate is simple. It uses crushing and grinding equipment to process calcium carbonate minerals into powders. These powders can meet industrial requirements. Each industry has unique needs for the size, shape, and color of ground calcium carbonate. They also need different particle size distributions. So, the tech for making ground calcium carbonate should consider the process route. It should also consider the choice of equipment. It should match the product’s positioning. Grinding equipment is designed based on different principles: impact, squeezing, friction, and shear. It can also use a mix of forces. Each design leads to different grinding effects and product fineness.
Common processing equipment for ground calcium carbonate is used in large-scale dry processes. It includes Raymond mill, Vertical mill, Ring roller mill, and Ball mill. The equipment has different crushing and discharging methods. So, the powder it makes differs a lot in grain type, particle size, and energy use. The product position also differs.
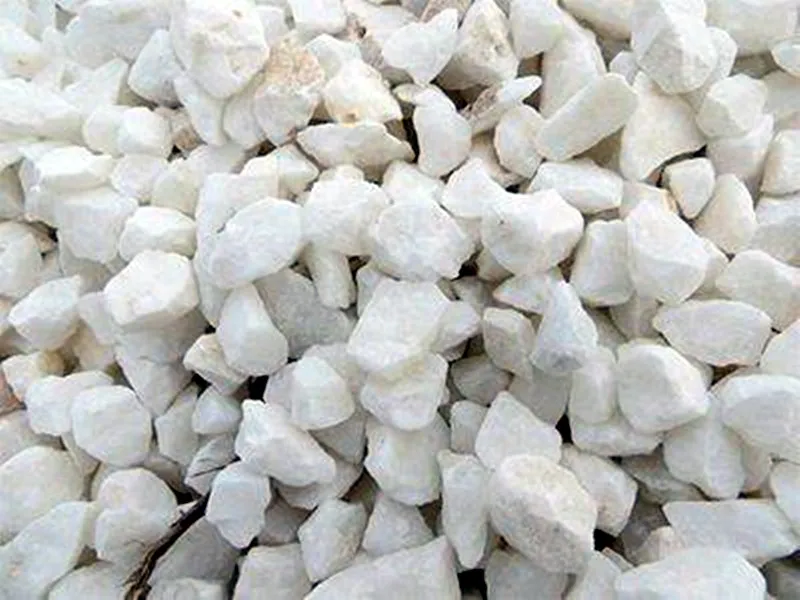

The ball mill can work with the air classifier to form a closed circuit. After grading, the coarse powder can be returned to the ball mill for re-grinding. The Raymond mill, vertical mill, and vibration mill cannot form a closed circuit. They have limited capacity and struggle to handle returns. So, they can’t solve the problem.
The ball mill is also low speed equipment. It minimizes energy consumption from impact and friction. It is not only ideal for grinding hard, abrasive minerals. It’s also the cheapest for grinding white filler minerals, like soft calcium carbonate.
Calcium Carbonate Ball Mill and Classifier Production Line
Features:
The product particle size control is flexible, special design is adopted to reduce noise and emission; Automatic control, easy to operate, According to the scale of investment, it provides personalized customized scheme and provides value-added services.
Application:
Calcium carbonate (calcite, marble, lime stone, chalk), quartz, zircon, paillite, barite, kaoline, dolomite, magnesite, alumina, super fine cement, slag, steel slag…
The Raymond mill, also called Raymond roller mill, combines grinding, classifying, and if necessary, drying, in one machine to produce precisely sized powders to meet exact production specifications. It is an efficient fine grinding machine for large-scale powder production.
Calcium Carbonate Raymond Mill Grinding Machine
Applied materials:
various non-flammable and explosive minerals such as gypsum, talc, calcite, limestone, marble, potash feldspar, barite, dolomite, granite, kaolin, bentonite, medical stone, iron ore, etc.
The non-metallic mineral grinding ring roller mill pulverizes non-metallic minerals into fine powder. It is designed and developed based on many years of research and experience in grinding mill production.
Ring Roller Mill
The grinding ring is fixed on the inner wall of the mill while the roller assembly rotates around the ring. As the roller assembly rotates, the material is fed into the mill and is ground between the grinding ring and rollers.
One of the advantages of the ring roller mill is its high grinding efficiency. The grinding ring and rollers are made of high-quality materials, which ensures a long service life and reduces maintenance costs. The unique design of the roller assembly also helps to increase the grinding efficiency by evenly distributing the material on the grinding ring.
Another advantage of the ring roller mill is its ability to grind various non-metallic minerals. It can be used to grind minerals such as limestone, calcite, marble, talc, barite, dolomite, etc…
Vertical mills (Table Roller Mills) crush by squeezing layers of material. The most fine can reach 1250 mesh. After sorting, the most fine can reach 3000 mesh. They generally suit materials with mohs hardness less than 7.
Table Roller Mill
The ultra-fine vertical mill is currently the super-large ultra-fine grinding equipment in Asia, which has been successfully applied in the market and has mature technology. It can replace imported equipment and is an ideal equipment for large-scale production of ultrafine powder with high efficiency, high yield, environmental protection and energy saving.
It is suitable for superfine grinding of non-metallic minerals such as calcium carbonate superfine powder, limestone, barite, calcite, kaolin, gypsum, pyrophyllite and graphite. It can provide high-quality fillers and additives for industries such as papermaking, plastics, coatings, rubber inks, and chemicals.